On-Site
ELECTROSTATIC PAINTING
Cost-Effective Electrostatic Refinishing for Businesses and Homeowners
Porcelain Patch & Glaze provides on-site or off-site factory refinishing for virtually all metal surfaces, with results that look and perform like new.
What is electrostatic Painting?
Electrostatic Painting, also known as Electrostatic Refinishing, is a type of painting that uses static electricity to create a pattern to refinish existing metal surfaces.
Electrostatic Refinishing is a method of spraying an environmentally compliant Low VOC Coating onto a metal surface. There is no overspray, and the process complies with all applicable environmental regulations and regulations.
A Cost-Effective Solutionfor Businesses and Homeowners
Save as much as 90% of replacement cost by utilizing Electrostatic Painting
What Kinds OF ITEMS CAN BE REFINISHED using Electrostatic Painting?
Using the Electrostatic Painting technique, items that can be refinished include, but are not limited to:
- lockers
- filing cabinets
- laboratory cabinets and laboratory furniture
- elevator doors and frames
- bathroom partitions
- manufacturing equipment
- safety railings
- aluminum storefronts
- curtainwalls
- metal stairs
- heater covers
- metal furniture
What types of businesses should use Electrostatic Painting and Refinishing?
To name a few, the electrostatic method is well suited for refinishing items and equipment for:
country clubs. hospitals. banks. health spas. gymnasiums. warehouses. laboratories.
FEATURED ELECTROSTATIC PAINTING PROJECTS
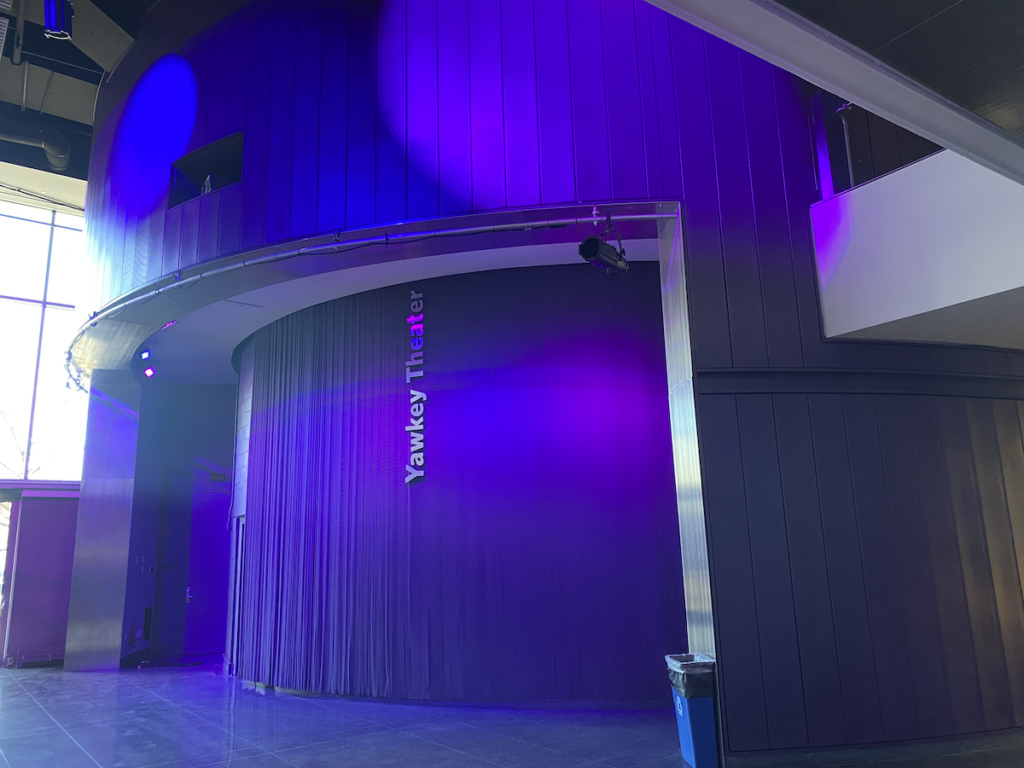
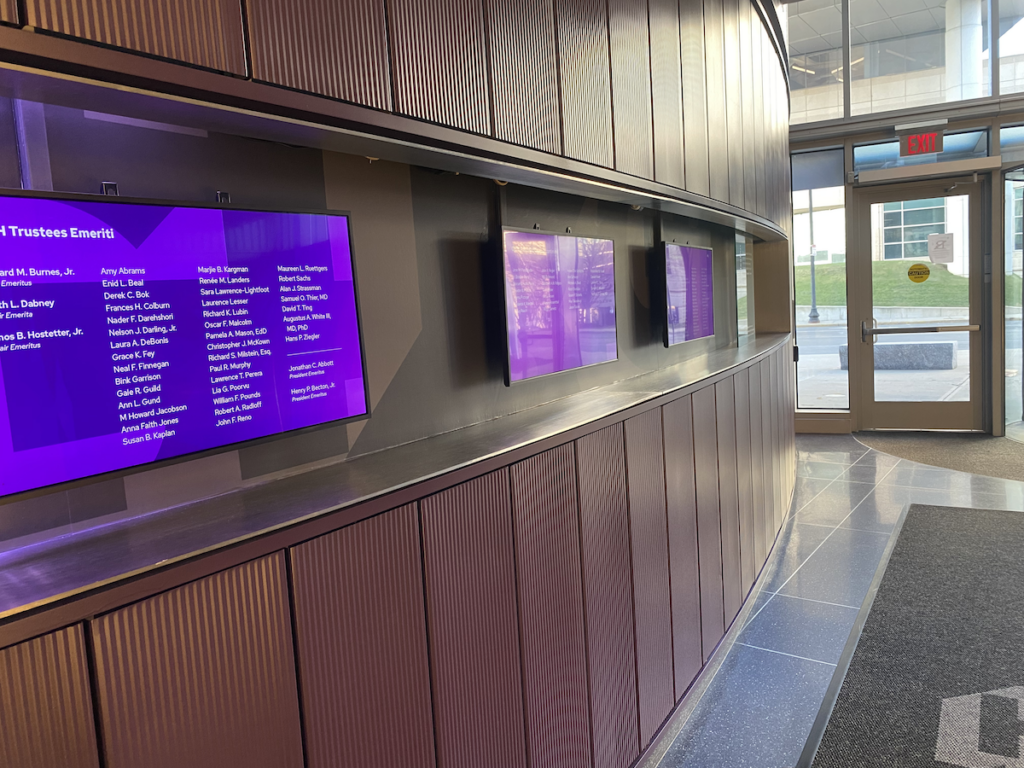
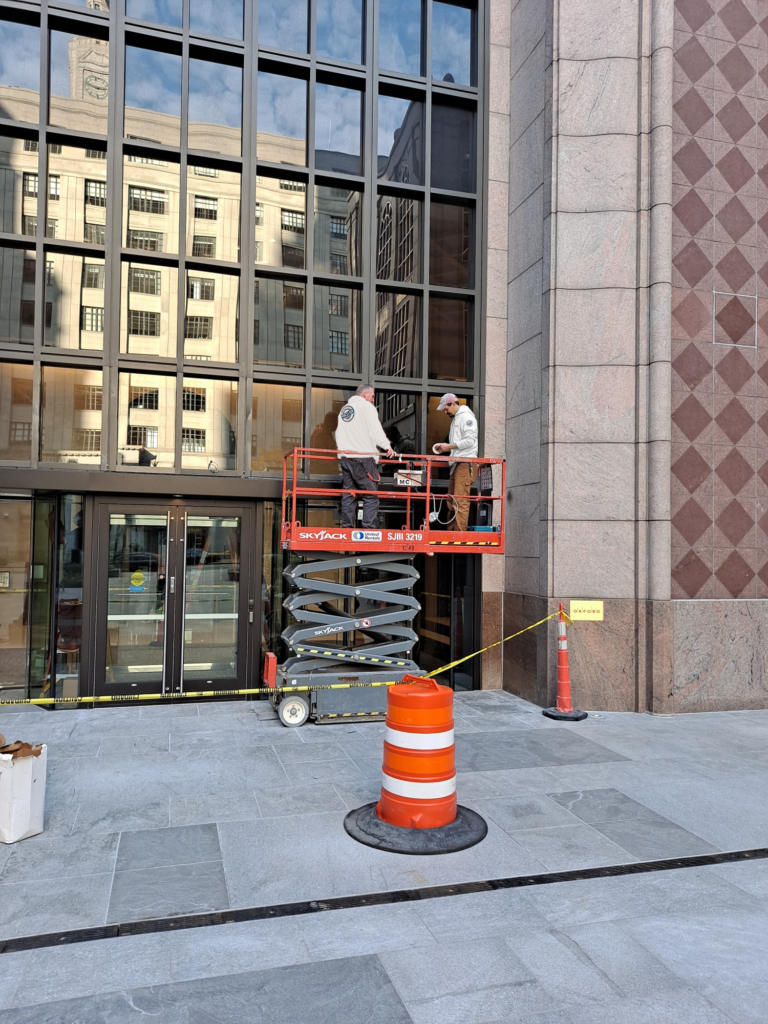
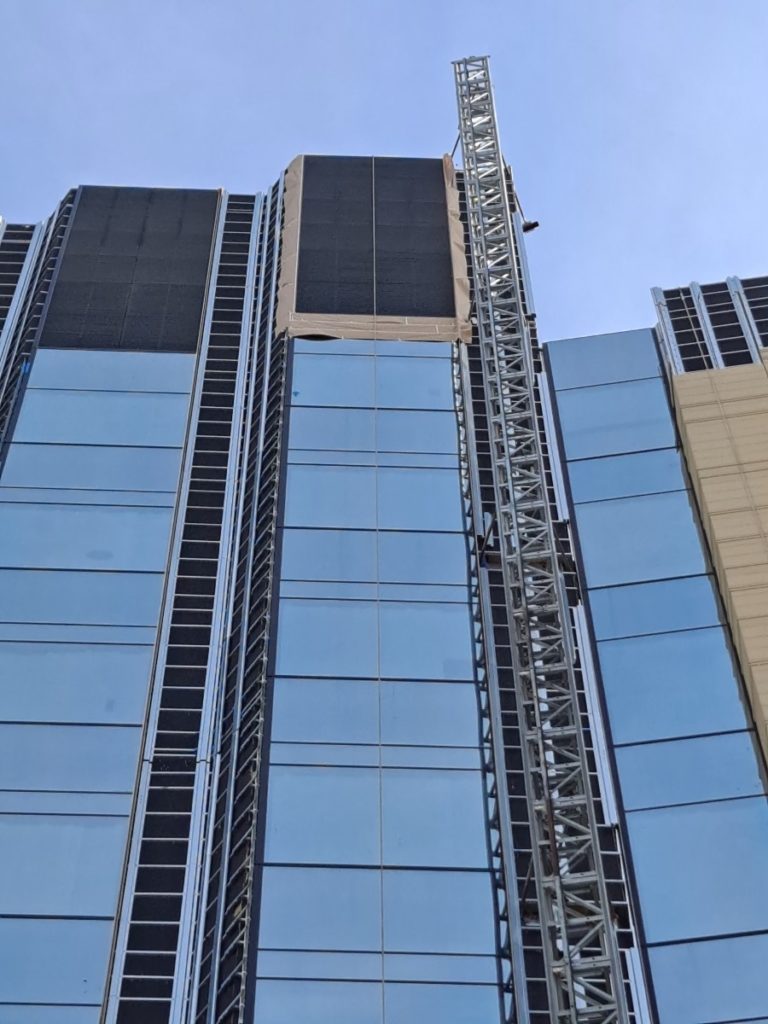
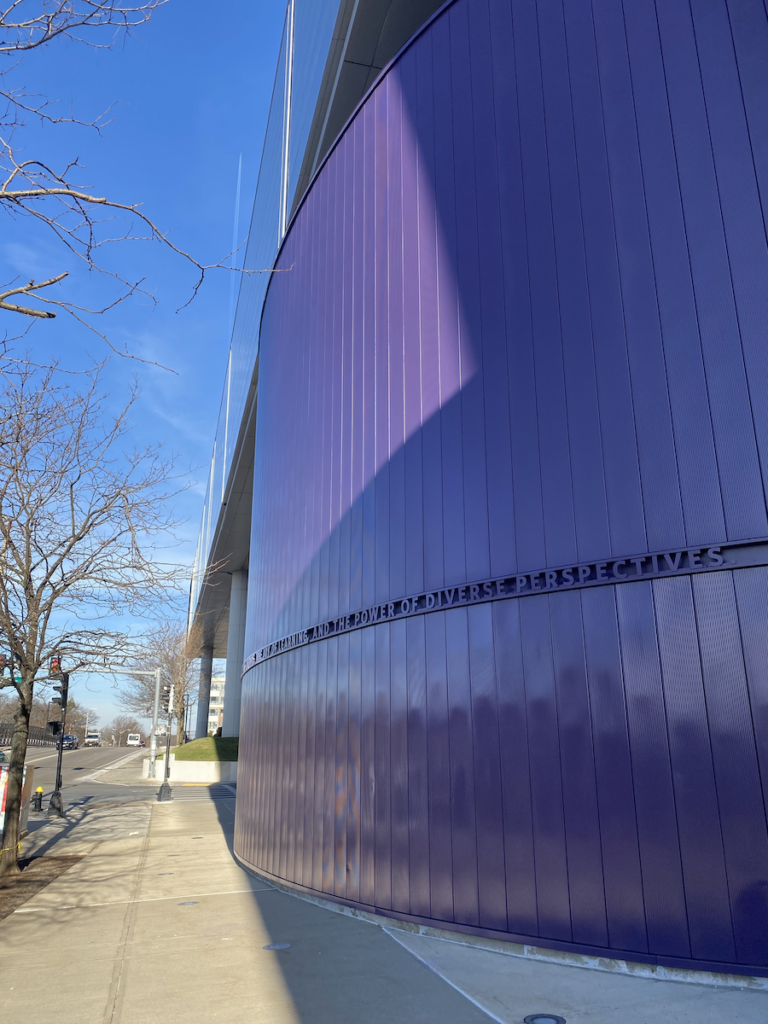
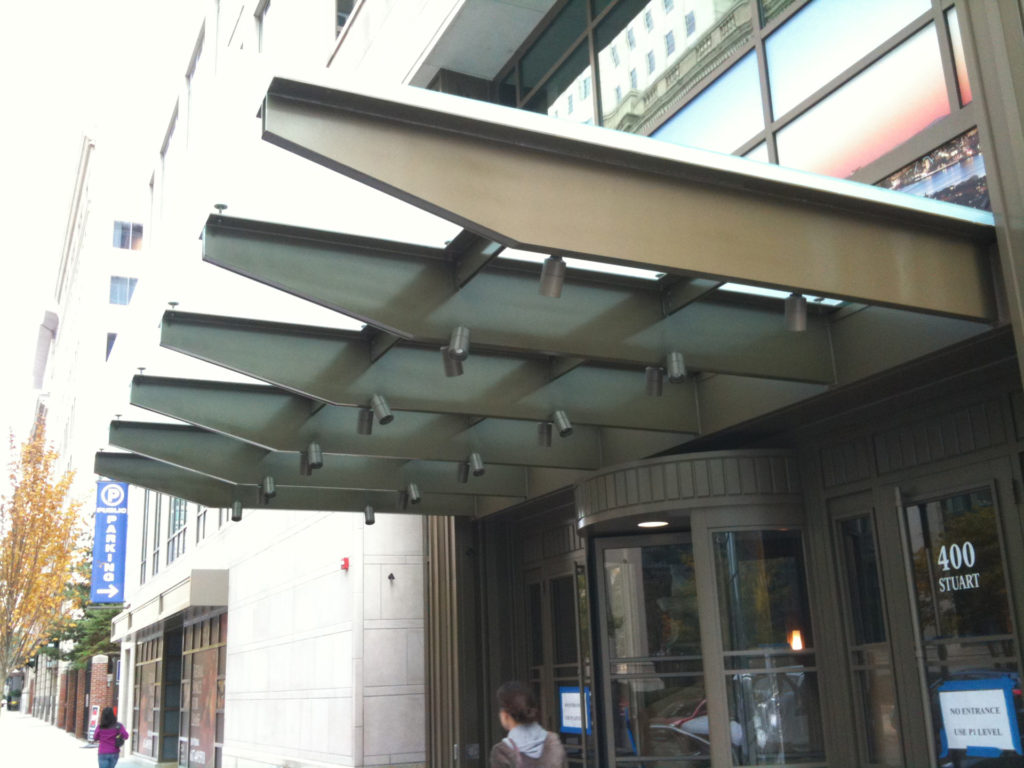
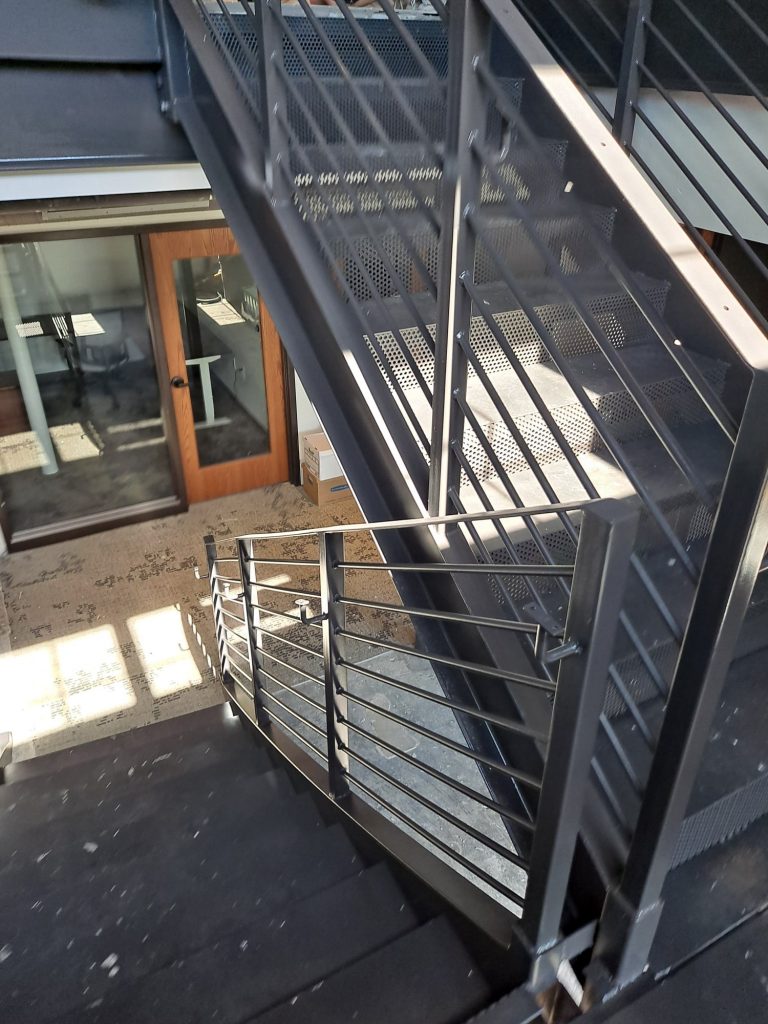